How power supply design can make for smooth operations
Like other electronic devices, today’s digital control systems rely on a direct current of steady, consistent incoming voltage to operate properly and reliably. But the AC power baseline typical of most industrial environments is neither steady nor consistent, being battered by sudden starts and stops of other electrical loads that propagate voltage dips and surges across the system. It falls then to the industrial power supply to smooth the voltage swings and current inrushes that can take their toll on system operation. To learn more about why it’s important to keep AC inrush as low as possible—and the steps that power supply manufacturers take to do so—Control caught up with Chris Harman, product marketing manager for PULS L.P.
Q: What exactly is an AC inrush current, and how are they detrimental to control system operation?
A: We’ve all experienced the effect of an AC inrush current in our personal lives, for example, when a refrigerator, a power tool, a vacuum cleaner or an air conditioner first turns on. The surrounding lights may dim briefly, a sign that the AC voltage is being drawn down due to the sudden demand for power.
Fortunately, in the home environment, flickering lights are typically as bad as it gets. However, in an industrial environment, inrush current has potential risks. It can have a negative impact on operating systems, with unexpected downtime or even damage to expensive equipment.
In addition, when selecting other system components such as circuit breakers, switches and relays, inrush current effects must be considered. This means that reducing the potential for inrush currents to affect the downstream side of the associated power supply also reduces the need for incremental system design and maintenance efforts.
Q: In what ways can power supplies mitigate the effects of AC inrush currents?
A: A switched-mode power supply (sometimes called a switch-mode power supply, or SMPS) converts the AC supply voltage to DC by way of a bridge rectifier. The voltage is then smoothed using a large electrolytic capacitor. When a DC device that is downstream of the power supply is first turned on, current “rushes in” to the input capacitors.
This inrush current is higher than the nominal or operational current of the power supply. Therefore, the inrush needs to be limited to ensure stable operation and to avoid tripping fuses or circuit breakers, generating voltage dips or welding relay contacts. There are various technological solutions and design techniques that can achieve a low inrush current.
Q: I understand that NTC, for “negative temperature coefficient” thermistors, are the easiest and least expensive way of limiting inrush current. How does this approach work, and what are its limitations?
A: This solution is based on thermally sensitive semiconductor resistors placed upstream of the power supply’s input capacitors. When power is first applied, the cold NTC thermistor has a high impedance and effectively limits the charging current to the capacitors. The NTC thermistor heats up very rapidly due to its own losses, so the impedance drops to a low level, allowing the required current to flow.
This simple solution has some disadvantages. If ambient temperature is too cold (e.g., below zero °C), current may not ramp quickly enough, and start-up problems can occur. If ambient temperature is too warm, the thermistor may fail to adequately limit the inrush.
Another weak point in NTC thermistor performance is after a short AC voltage interruption: As soon as the AC voltage is interrupted, the electrolytic capacitors are discharged but the NTC thermistor remains warm and at low impedance. Therefore, it’s practically ineffective if AC power is quickly restored. This effect can cause nuisance tripping of fuses or circuit breakers. Also, the very nature of NTC thermistor performance introduces power losses that lower the overall efficiency of the power supply.
Q: Are there other ways to limit inrush current that sidestep the disadvantages of NTC thermistors?
A: The first of three approaches is with a fixed power resistor that is automatically bypassed when the power supply capacitors are fully charged. This approach may rely on relays, TRIACs (for triode for alternating current) or IGBTs (for insulated-gate, bipolar transducers). This approach is significantly more complex and expensive than NTC thermistors, so is primarily used in power supplies with higher power designs (250W and above). The advantages are that fixed resistors are insensitive to ambient temperature effects and incur significantly lower power losses.
Similarly, trailing-edge phase dimming bridges the current to the capacitors with a relay after charging is complete. What makes this solution special is the limiting part itself. An electronic system measures the instantaneous value of the AC voltage and compares it with the voltage of the partly charged capacitors. If the difference is less than a set threshold (e.g., 30V) a MOSFET (for metal-oxide-semiconductor, field-effect transistor) closes. If the difference is greater than 30V, the MOSFET remains opens.
When on (closed) the MOSFET thereby limits the peak charging current. For example, if the on-resistance has a value of 4 ohms, the current is limited to 7.5A (30V/4 ohms). A gentle start for all input voltages is therefore guaranteed. If the input capacitor is fully charged the inrush current limiting circuit is bridged to avoid power losses. PULS uses this technique in many of its Dimension C Series power supplies.
The third method, pulse charging, is a smart and efficient way of softly controlling how much energy is allowed to charge the input capacitor. To achieve this, a small switch-mode power supply is integrated and used as a charging circuit. This enables a very efficient charging of the input capacitor with no losses.
This method leads to several advantages:
- The inrush current is only slightly higher than the normal operating current.
- The peak current can be defined more accurately, as there are no variables involved.
- A delay on the charging is also incorporated into the design. This means when power is initiated or restored, the supply does not contribute to unnecessary inrush as neighboring equipment is also energized.
- Fuses or circuit breakers can be sized for operating current and not peak current.
- The inrush current limitation is independent of input voltage or temperature.
Pulse charging is highly efficient and is used in many DIN-rail power supplies is the PULS Dimension Q Series.
Q: How can one best decide the optimal choice among these four methods of controlling inrush current?
A: Functionality always comes first. But when faced with alternate solutions that can do the job, total cost of ownership (TCO) is always the rational decision-maker’s first tiebreaker. Indeed, devices with lower up-front costs typically penalize their owners in more ways than one. The TCO calculation for a superior design that results in lower energy usage is typically sufficient from an economic justification perspective.
Further, a power supply that produces a very low AC inrush current when it's energized can allow more power supplies to be operated from a single circuit breaker, reducing the number of overall components in an enclosure and possibly resulting in a smaller control cabinet. Lower AC inrush can also help reduce voltage dips on the AC mains if several supplies are turned on at the same time—especially if other AC equipment is being energized at the same time. This also prevents nuisance trips that can cause unnecessary downtime and troubleshooting efforts.
Low inrush current, taken together with other power supply features such as active power factor correction and higher short-term output current can significantly reduce the overall size and rating of the necessary power supply and help reduce mains disturbances. Which one is the right one for you depends on your application and in which environment it is used. You can also consult our team of skilled application engineers to find the best power supply for your application.
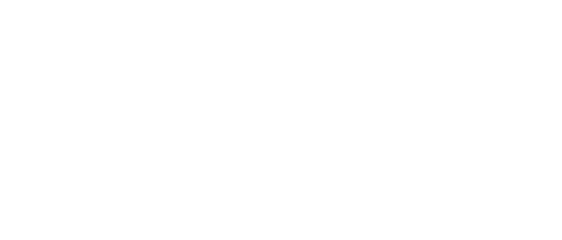
Leaders relevant to this article: