By Nancy Bartels, Managing Editor
Predicting the future is always risky business. Im still waiting for the flying car I was promised forty years ago. Many, if not most, technology predictions, such as that flying car, are wildly inaccurate, and yet, we never seem to see ahead of time the game-changing developmentscan you say Internet?that catch everybody off-guard, leaving us gasping for air and struggling to find our footing in the new situation.
At the same time, as the saying goes, the more things change, the more they remain the sameespecially in the notoriously conservative process automation industries.
Dick Caro, CEO of automation system design consultancy, CMC Associates, and a member of the Process Automation Hall of Fame, says, The plant of the future will look like the plant of today. There wont be much difference in chemical or petroleum processing.
For one thing, you cant change the laws of physics and chemistry. Peter Zornio, chief strategic officer at Emerson Process Management, reminds us, The processes themselves cant change. Most things will look the same unless something totally unforeseen happens. Its not like were saying all these plants are going to be differentnot in 10 or 15 years.
Few companies will rip out a tried-and-true system for something untested, no matter how gee-whiz it might appear to benot without a sufficient track record in the field―and by the time a technology has that track record, its hardly brand new anymore.
In fact, much 2025 technology is here now, at least in beta or version 1.0, but we wont see its real impact for another decade or so.
Caro points to the case of fieldbus technology. Fieldbus has been on the market for 14 years, and we still dont use most of the technology thats available to usnot because its difficult or unavailable, but because of the conservative nature of the industry.
That said, the hardware and software that will run Factory 2025 will make it a very different place to work.
Check Out the Best Buy
Alex Johnson, solutions architect at Invensys Process Systems, sees hints of what future control rooms will look like in the home entertainment aisle. The PC control industry tracks the home entertainment industry. When we got color TVs we had to update HMI to color. When video games came along, operators began to expect those kinds of graphics. HMI hasnt changed significantly for 20 years, but look at home entertainment. Thats what our HMI is going to look like.
Benson Hougland, vice president of marketing at Opto 22 looks to the Internet for a preview of what will happen in automation. Automation tends to follow advances in the IT space by one or two decades, he says. What the Internet did is facilitate communication. Its a way of moving communications and intelligence into far-reaching areas, giving devices a way to communicate and understand. It ultimately changed commerce. Were going to start seeing more of that in the factory rather than traditional DCSs. You might have PLCs ultimately be the decision-makers. Were going to see a fundamental shift to more autonomous devices that know how to acquire, consume and make decisions about information.
In the same vein, simulation software will come to look more and more like your kids video games and play a bigger role in the control and training rooms. (See Lets Pretend sidebar at the end of this article for more on simulation.)
All Wireless All the Time
The biggest sea change in process plants will be a subtraction rather than an addition. What today is wired will be wireless, says Caro, echoing all the prognosticators we talked to.
Wireless is the Internet of the process plant, says Emersons Zornio. There are only a few game-changing technologies, and wireless is going to be the one for the next eight to 10 years. We dont know what the wireless apps are going to be. Think of the Internet. We all fixated on email first. It wasnt about MySpace or YouTube, paying bills online or working from home. All these apps started coming out as the Internet grew in capability.
But the dirty little secret of current wireless technology is that it isnt really wireless. At some point, every wireless device has to be connected to a power source. The real game changer, what Zornio calls the last frontier of wireless, is breaking that connection.
Increasingly powerful, but smaller batteries, such as are found in cell phones, are one way to solve the problem, he says. Another way is micromachine technology. Visualize a whole little internal combustion engine the size of a D cell battery running on very little fuel, or one that actually siphons natural gas out of the lines its running on, and it runs forever.
Steve Baker, control system specialist at JNE Automation, Hamilton, Ontario, and a member of Rockwell Automations, Advisory Board, says, MIT [Massachusetts Institute of Technology] is currently developing technology to wirelessly transmit low-wattage power to devices within a 10-foot radius. If this technology was improved, smart field instruments that used wireless communication and power could populate a facility without the need for any wires or conduit.
This wireless world has other implications. James J. LaBounty, associate director at Wyeth Biotech, Wilmington, Mass., another Rockwell Advisory Board member, anticipates that sensors out in the process will have no direct power connection, just induced power to the sensors and transmitters. Well also have digitized control and monitoring signals to the controller and diagnostic and calibration data to the maintenance monitoring systemsagain, no field wiring or I/O modules. Well also see an extensive use of 2D bar code and RFID to track production, people and equipment in the plant.
Collapsing Architecture
Steve Ryan, global product general manager for GE Fanuc Intelligent Platforms, predicts a collapse of familiar hierarchies and boundaries in software architecture. He also sees the long-promised absolute seamless visibility up and down the organization and into the supply chain finally coming to fruitionalong with KPIs and metrics in real time. Driving these developments will be the need to compete in a flat, global economy that requires extreme cost-effectiveness from every plant. If a plants still going to be there, this will be a necessity, he says.
The walls between enterprise, manufacturing execution systems (MES) and plant systems and between information and automation architectures also will collapse, he says. Technology will advance so that things that could only be done with separate architecture in the past will be unified in the future.
One of our prognosticators, who didnt care to risk the wrath of the true believers on both sides of the enterprise IT/plant automation wars, suggested that IT would be the winner, predicting that automation down to the DCS level will be subsumed into general IT and become just another form of IT specialization. There will be a director of automation in the IT department, he says.
Furthermore, manufacturing business applications and tasks done by MES and SCADA systems today and separately in multi-function process controllers will merge into one cell controller, predicts Wyeth Biotechs LaBonty.
Baker adds, If field devices are sufficiently intelligent, we may be able to get away from having a PLC or DCS brain and simply network the relevant devices together and write programming that is shared by whichever device is required.
Sensor DNA and Electronic Noses
Those sufficiently intelligent devices may include such forward-looking gadgets as electronic noses, says Invensys Alex Johnson. People are making electronic noses that can detect low concentrations of materials and report back what they are very quickly. Theyre chemical sensors that work like a nose. They detect odors in the air. They bind with the DNA on the sensors. Youre seeing a need at the customer level to know more about whats going through the pipe, and that need, plus the technologies that are available in other areas, are going to make for a change in sensor technology. Were going to go beyond temperature, pressure, flow and the occasional density reading.
Wendy Foslien, a researcher at Honeywells Automation & Control Research Lab, says looks to nanotechnology to change the way sensors operate. If you start thinking about very small sensors, circulating through a process, we can begin to sense things weve never been able to sense before. What if you could get inside the material you were producing? As things get smaller and costs get lower, youre no longer tied to control room, and that opens up all kinds of new possibilities.
No More Valves
Meanwhile, Dick Caro looks forward to the possible disappearance of valvesone of the most vulnerable spots in current process systems. He says, They are at the root of most control problems. Stickiness causes leaks and unstable controls. It would be nice to do away with them.
The incentive for doing this, he says, is energy savings. Flow control consists of pumping up a liquid to pressure and taking the pressure drop across a valve. Thats a complete waste of energy.
Tom Edwards, senior technical advisor at Opto 22, also visualizes the disappearance of valves. [A valves] purpose is to control the direction or amount of flow. Thats being done today by variable-frequency drives to control the speed of the pumpa technology that wasnt available a few years ago. This kind of evolution in the way things are done could make a PID valve or controlling a loop obsolete.
Another basic process Caro would like to see improved is distillation. In petroleum and chemical refining, we spend a lot of money on energy for distillation, he says. More than 40% of energy consumption is spent on distillationmore than on automotive gasoline. The driving force [of distillation] is heat energy, inserted in the bottom of the column and released at the top, and that heat is lost. Im hoping some people can develop ways to recover more of that heat energy. I hope that in 15 years well be able to do something about this. I have no idea what that something is; I know the problem, but not the solution.
Remote Control
Fieldbus began the drive to remote operations. Wireless technology continues to power it. Now combine wireless with Internet connectivity in the plant and more and more computing power on the devices themselves, and suddenly plant-floor operations begin to look a lot different.
JNE Automations Baker visualizes small flying surveillance drones sending video feeds back to monitors in the control room. He suggests that they could be connected wirelessly to field instruments and able perform detailed diagnostics and enable maintenance personnel to remotely control them to perform simple repair/replace procedures.
Sound too George Jetson-ish? Baker points out that the military is already using remote-controlled planes and vehicles, and chances are good that such technology will leak into the industrial environment.
The other obvious place for drones or robots is in dangerous areas. SIL-2, 3 and 4 areas will be manned by robots, says LaBonty. Humans wont be asked or expected to take on hazardous or dangerous tasks.
But remote access will have more pervasive and ultimately far-reaching effects on the control room. Steve DeVries of Invensys visualizes a tactical control room in addition to the operations control room. This would contain a group of specialists able to see the same information the control room operators see and offer advice and make decisions about plant operations. This is one way, he says, to overcome the dearth of trained process professionals that the industry is already grappling with.
One control room for multiple plants is another likely scenario. New process control architectures will allow this, Brandon Henning, global industry manager for food and beverage for GE Fanuc, says. What youre going to see is a retooling of process control. You will have a cockpit from where you can run 10 plants. Companies will be able to leverage the investments theyve made without having to completely retool.
This remote control is predicated on different ways of handling information. The interesting thing will be to concentrate the information flood, says Gerd Ulrich-Spohr, strategic technician for industry automation at Siemens Energy & Automation. If you have a lot of data, you have to shrink it to something that you really want to know. Often you have information about the temperature or pressure, but what you really want to know is the state of the process. What will be very interesting is if we manage to combine the available information and change it to information that is really needed and tells us more about the state of the process, rather than the details of the data.
Invensys DeVries sees a merging of two data models to build one version of both business and process control truth. Plant-floor workers are trained to think in terms of a loop. If the loop isnt wired correctly, you cant do anything else. Office knowledge workers dont think of a loop, but they have a sense that the data is soundthat there is one version of the truth. Several of our clients are merging these two ideasdeterminism on the plant floor and the IT idea that the data, wherever it is has to be secret and private and trusted.
Commander LaForge to the Bridge
With all that information from not just the sensors, but from the rest of the local plant and other, remote locations, HMI will acquire a whole new look. The over-riding vision is one of all human interactions coming via a single HMI, supplying users with only the information they need when they need it. DeVries says it will be almost like an ATMreliable around the clock and available only to the appropriate people.
This single point of data contact may be a fashion statement of sortsthe wearable HMI. I find it amazing that we havent already gone in this direction, says Steve Garbrecht, director of product marketing at Wonderware. The idea that I have to have a PC on my desk or a flat screen in a control room seems nonsensical. The first person who comes up with a PC device thats really lightweight, like a pair of sunglassesthat makes it really usefulwill not only have a business device, but an automation productivity device.
Steve Baker fills out the vision. He sees a wireless HMI clientsome type of LCD glasses that would display the facility layout in a 3D-rendered view that changed, via GPS, based on the persons locationconnected to the processes while the wearer wanders the facility. Vocal or sub-vocal commands or some small text-messaging keyboard on a wrist band would allow the interface to monitor or control the process so the operator would never be out of touch with plant operations.
Robert Fretz, head of process automation and MES for F. Hoffman-LaRoche, suggests, No more control roomsoperators would simply input process changes through their PDAs.
Rick Dolezal, manager, global marketing for the process business at Rockwell Automation, says Geordie LaForge glasses (like those worn by the blind helmsman on the Star Trek series, who wore a prosthetic device wired right to his brain that allowed him to see) are just the next step in remote operations. Wastewater treatment plants already run 24/7, but we send people home at midnight. If theres a problem, they can get out of bed and check remotely. Just take it another step. You have these glasses where one eye is the HMI and the other is clear.
If the thought of walking around with an HMI screen fixed to your eye makes you a little nuts, remember that Plant 2025 is also going to be employing younger engineers with a whole different attitude toward information access.
Wonderwares Garbrecht says, People say this is too distracting, but younger people have no problem multi-tasking. They can have a full conversation while theyre texting someone. Twenty years from now people are going to ask, Why did they have these things on their desks to look at information or carry these things around on their belts?
Dogs Rule?
The old joke is that the plant of the future will employ one operator and a dog. The operator will feed the dog, and the dog will prevent the operator from touching any of the controls and messing up the system. The scenario is unlikely, says Stan DeVries, director of operations management solutions at Invensys Process Systems. In some areas like power generation and oil and gas, some plants run almost without staff now, but thats not a vision for the process plant of the future, he says. What well see instead is, about the same number of workers 10 to 15 years from now, but what they will do will change quite a bit.
Like DeVries, Emersons Peter Zornio predicts the process automation plant will have fewer people, especially in hazardous areas, but he adds. Nobody believes theres just going to one person. There will be a few people, knowledge workers, backed up by a cadre of detail experts in some central location like a central engineering office or the vendors office. Theyre going to be using tools like video conferencing, wikis and high-tech search engines to troubleshoot detailed problems in areas they dont know enough about.
Dave Emerson, principal systems architect at Yokogawa, goes one step further to the retirement home control room. He visualizes connections to retired process control experts who can see what the young operators see and help them interpret the information. Retirement is no longer a barrier for a lot of people, he says. That knowledge will be easy to tap.
Kevin Zaba, process automation business director at Rockwell Automation, says, The role of line operators is going to change considerably. They will become more directly responsible for the financial results of the plant, with their view into the process converted from engineering units to financial measures that align with the KPIs of the plant.
Siemens Ulrich-Spohr adds, Operators will become much more than operators. All the low- level tasks will be carried out by the system, so the operator can make business decisions about how to run the plant in an optimized way.
This will lead to a different kind of worker and a different kind of education. Users are going to be much smarter from a big picture level, says Dolezal. Theyre going to have degrees that dont even exist now. Therell be a thing called a manufacturing management degree that combines electrical engineering, accounting, business and computer systems all in one degree.
The new process plant workers will also come from more diverse educational backgrounds. Stan DeVries says well see not just business school grads, but those with liberal arts and psychology in the new control room. The traditional guys are not going away, but the group will be different and more diverse, he says.
It will also be a bit tougher for the operator without a four-year degree. Theres a shift from community college to full engineering in the control room. Theres still room for the community college folks, but their adjustment is difficult.
This sea change in the nature of process plant jobs may well have more impact on changing the control room than any of the whiz-bang technology in the pipeline. Different kinds of jobs mean different kinds of workers. The young people waiting in the wings also have different expectations about their jobs and different ways of processing information. But thats another story. See our September issue for Process Worker 2025.
Modular Process PlantsNot every iteration of Plant 2025 will be a giant facility with remote operations spread over acres and acres and building and start-up costs running well into the millions. Yokogawas Dave Emerson speculates that a model with its origins in the automotive industry may well put in an appearance in process manufacturing, particularly in developing countries. Its not uncommon for suppliers to automakers to locate small factories near their customers operations because that eases the cost of getting products where they need to be and enables just-in-time manufacturing. Emerson says the same model may appear in process operations. Furthermore, he adds, What were going to see in 10 or 20 years is that the global economy will continue to grow, and countries like China, India, Brazil and Africa will have increased demand for all kinds of goods. What if you could build modular, skid-mounted factories and chain them together? That would give you the capacity you need and the ability to place the facilities close to where they need to be. The challenge for developed countries, he adds, will be to build these small-scale plants where they need to be. Its a model not unlike the micro-lending that takes place in developing countries. In India, Proctor & Gamble already builds shampoo-mixing facilities small enough to place in a garage, provides the operators with the raw materials and sells the products locally. |
Lets PretendSimulation in process plants is coming into its own as a tool for training, for optimization and for process modeling, says Paul McLaughlin, director of Honeywell Process Solutions architecture. It will be exploited in operator training, the creation of process control solutions and in process dynamic modeling. he says. He adds that we will see significantly better fidelity in simulation systems, to the point where they can mimic the process experience exactly.The kicker, however, is that the more realistic you want your simulations to be, the more computer power you will needmore power than the average process plant can afford. Running [process simulation] models now can be constrained by in-house CPU. Companies are constrained by what they can afford to purchase, says Jim Strilich of Honeywell Process Systems technology architecture team. Strilich sees in the future massively parallel computer resources made available on an as-needed basis through on-demand mesh computing. A company could go online and buy huge amounts of computer power it could never afford full-time for a few hours to run a necessary simulation. Again, the technology for such computing is here already. The SETI@home project of SETI (Search for Extra-Terrestrial Intelligence) has signed up some 5 million computer users in 200 countries to donate processing power to analyze radio waves in space for signs of extra terrestrial life. According to the Berkeley Open Infrastructure for Network Computing at the University of California at Berkeley, seti@home achieves an average throughput of 387 teraflops, making it equivalent to the second fastest supercomputer in the world. You can simulate a lot of processes with that kind of computing horsepower. |
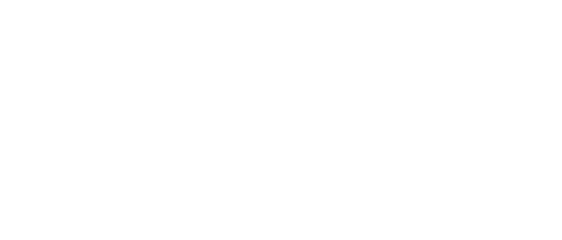
Leaders relevant to this article: