QUESTION:
I'M TRYING to figure out if a PID loop can be used as described below without having to change the loop gain when the number of pumps used is changed.
In our process, softened aluminum billets are pushed by a ram through a die in an extrusion press to create long, thin parts. The ram cylinder is powered by six hydraulic pumps, and the ram speed is determined by the total fluid flow from the pumps, which is determined by the pump stroke (how far the valves supplying fluid to the pumps are opened). Theoretically, the ram speed set point would specify the pump stroke required, and no feedback loop would be needed. But in practice, a PID loop adjusts the pump(s) to maintain the speed set point.
Our proposed control strategy is as follows: the total pump stroke required to achieve the ram speed set point is divided between one lead pump and other base pumps. The lead pump is controlled by the PID loop, runs in manual at 50% stroke during breakthrough, and then the PID loop is put in auto when the ram moves during extrusion. The remaining stroke is divided among the base pumps. For example, if the total required stroke is 160%, the lead pump is started at 50%, and the remaining two base pumps are run at (160 50)/2 = 55%.
Does the process gain change significantly when the system is using a different number of pumps? I believe the answer is no. I think a change in pump stroke from 150% to 200% should produce the same change in ram speed as from 450% to 500%. Is my thinking correct? If the process gain doesnt change, does that mean the loop gain shouldnt have to be changed once it is tuned up? Of course, the broader question is whether this is the best way to control the ram speed using the pumps.
In addition, the six hydraulic pumps that supply the ram cylinder are identical. Disregard load and assume hydraulic flow from the reservoir through the pumps to the ram cylinder occurs per design, and isnt hindered by the resistance on the other side of the ram. In round numbers, each pump can result in 20 in./min at full stroke. If one base pump (run manually) is on at full stroke, the cylinder is moving at 20 ipm, and the lead pump (run with PID) is at 50% stroke, the ram will now go 30 ipm. If two base pumps are on full stroke, the ram is moving 40 ipm, and the lead pump comes on at 50% stroke, the ram will move at 50 ipm.
The definition of process gain I am working with is: K = (change in transmitter signal) / (change in controller output). With one base pump at full stroke (20 ipm) and the lead pump at 50% stroke (10 ipm), the ram speed will be 30 ipm. If the controller goes to 100%, the ram speed will be 40 ipm, the change will be 10 ipm and the gain will be K=10/50 = 0.2.
With two base pumps and the same change in lead pump, the change in ram speed is from 50 ipm to 60 ipm, and the calculation for K gives the same result. Doesnt this mean the process gain is the same as long as only one of the pumps is controlled by the PID loop, regardless of the number of base pumps?
William Love
ANSWER:
THE GOAL of tuning most process control loops is to obtain quarter-amplitude damping. This will result if the product of all the gains in the loop equals about 0.5. This result is achieved through tuning, which is the process of finding the controller gain, which will make the overall loop gain 0.5.
The controller gain (and most other gains) consists of a steady-state component (Kc = the proportional setting), which is unaffected by the period of oscillation and the dynamic gain (gc), which varies with the period of the input (error) sinusoidal. The (Kc)(gc) product is the total gain of the controller (Gc). Therefore, slow processes can be controlled with high-gain controllers, while controllers on fast processes must have low gains.
In this example, (Gc) = 0.5/(GpxGvxGt); Gt = 100%/(transmitter span) = 0.83 %/in. if transmitter span is 0 in. to 120 in. and if the transmitter is linear; Gv = maximum flow/100% = Constant, if the final control element is linear; Gp = (change in speed)/(change in pump flow) This is constant if we disregard the base pumps, which can be okay if all pumps are installed identical and if Gt and Gv are as above.
In a flow process, the process gain is high, and the controller gain must be low. The higher the controller gain, the more corrective action the controller can apply to the process in response to a small deviation from set point, and the better the quality of the resulting control will be. Unfortunately, if the gain product of controller and process reaches unity, the process becomes unstable, and undampened oscillations (cycling) will occur. Therefore, it isnt possible to tightly control fast (high-gain) processes without cycling.
The loop gain is the product of all the gains in the loop, including sensor, controller, control valve and process. In a properly tuned loop, the product of all these gains is 0.5. In your case, the process gain is the ratio of a 1% change in the manipulated variable (m = the output of the speed controller) and the resulting change in the controlled variable (c = the speed change of the ram). If I assume that when one pump is on, this ratio (Gp = c/m) is one, then, (because the ram displacement and speed rises with the volume of flow), if two pumps are on, Gp = 2c/m, etc.
As the load rises (as the number of pumps in operation increases), the process gain drops, and the controller gain also can rise (proportional narrow). Tuning such a system can be a problem because, to arrive at an overall loop gain of 0.5, the controller should apply a high gain when the load is high and a low gain when the load is low. Therefore, if the loop was tuned (controller gain was selected) at high loads, the loop will cycle when the load drops, and if the loop was tuned at low loads, the loop will be sluggish when the load rises.
Béla Lipták
ANSWER:
MY FIRST question is how tight a control is needed, i.e. does the ram speed directly impact the quality of the extrusion product? If control doesnt need to be very tight, then the proposed scenario might work, assuming that the total resistance for each pump is similar, and each pump performs in the same way. In mentioning total resistance, my concern is that identical pumps can certainly be manifolded together in a way that is balanced or in more challenging designs that are very unbalanced, with widely different distances and resistance barriers (piping size differences or changes, elbows, etc.). Different types of pumps are more or less prone to issues with the resistance.
Assuming that the speed is critical, I have a couple general concerns: namely, 1) the relative performance of each pump; 2) levers for the operator to adjust limits; 3) situations that will credibly occur where one lead pump is not sufficient; and 4) the inferred stroke from the valve position.
When Ive run across multiple-pump systems in the past, I had systems with pumps of widely different capacity and response curves. For tighter control, I generally linearized the output for each pump. In cases of widely different capacity, Ive run plant experiments to set different gains on the controller, depending on which combination of pumps was running. I also generally had issues where either chronically or during abnormal situations, a given pump might need to be derated (or limited to a different capacity). I generally put in an Automan station, where the operator can manage a manual bias to handle this derating. I often put in low-pressure or flow overrides that will put a second and at times multiple pumps into CAS-to-controller to respond to larger upsets (including trip of the lead pump).
What would the proposed controller do when one of the base pumps tripped offline, and the capacity of the lead wasnt sufficient? What would happen if the lead pump tripped offline? Can the process respond fast enough to move other pumps into the PID control and respond before the process excursion warrants a trip? Does the amount-to-base-load get continually recalculated? Finally, I have generally used a direct flow measurement in these cases to have some process feedback (rather than relying on the inferred flow from the source valves). What happens to that inferred flow as the valves wear or as leaks develop in the system? Direct measurement of the stroke would likely improve reliability.
In terms of gain, this might be a place to use a gap gain, leaving slow response close to set point, and then use a stronger gain outside the gap. It also might be interesting to continually recalculate the base-load set point and use the lone lead pump as the trim controller.
In addition, in the control scheme that you mention, it seems to me youre just measuring the gain of one pump at a time (the lead pump). If all the base pumps deliver the base load perfectly, and all the pumps individually respond the same, and the pump curve ends up being linear across the span that you operate (so 1% of output change results in the same stroke response across the curve), then the gain should effectively be about the same. I have rarely found that type of perfect balance in practice.
When you talk about sluggishness or oscillation, the issue that immediately comes to mind is dead time. Are the pumps close to the extruder, etc.? Beyond that, it might be something inherent to the mechanical specifics, perhaps some sort of mechanical backlash or valve stiction.
Bridget Fitzpatrick, principal technical consultant, [email protected]
About Ask the Experts |
Continue Reading
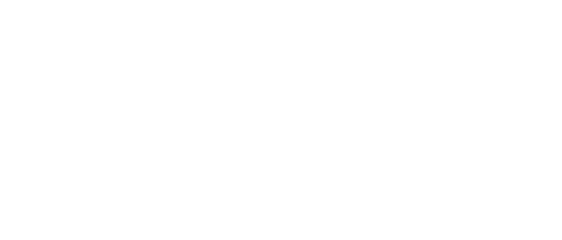
Leaders relevant to this article: