[sidebar id =1]All control engineers and process professionals know automation brings big value to their companies. The difficult question is how big?
"The challenge is convincing the business side of the company to provide the resources and money to improve automation," said John Wheadon, process automation manager at Dow Corning Corp., a wholly owned subsidiary of The Dow Chemical Company, during his June 29 presentation, "Key Steps to Improving Level of Automation for Control System Migrations" at the Siemens Automation Summit 2016 in Las Vegas. "We have to convince people that automation has value. To do that as automation professionals, we also have to use sales and marketing skills as well as technical skills."
Though it's a global leader in silicones, silicon-based technology and innovation with more than 7,000 products and 25,000 customers worldwide, Wheadon reported that Dow Corning was struggling to support its control systems, including many installed in the 1980s-90s. Even worse, before 2010, the company's process automation platform decisions were site- and project-based, which led to a large mix of platforms globally.
"Similar to many manufacturing industries, we were facing new challenges," said Wheadon. "The control systems installed in the 1980s and 1990s were getting old and unsupported. Lifecycles for new platforms were being compressed, driven by commercial off-the-shelf (COTS) and the Microsoft/IT model. Cybersecurity demanded we focus more effort on system integration security. And, resources and dollars for automation were increasingly constrained."
The obsolescence trap
Besides these forces, Wheadon explained that Dow Corning also became more focused on maintaining its control assets than leveraging new automation capabilities to create business value.
"We were putting in new systems and controls, but the plants were running the same. We were spending time and money, but really just standing still," explained Wheadon. "We kept the equipment running, but didn't improve it. Adding I/O or a new controller had no real value. We didn't ask if a faster processor or new software version would increase a plant's operating profit. We were at risk of process automation turning into a maintenance function by focusing more on keeping things running than leveraging automation for competitive business advantage."
[sidebar id =2]Wheadon added that it’s relatively easy to convince a business it needs to spend money to address obsolescence because that risk is understandable and quantifiable in financial terms, such as the cost of an hour of downtime to a business. "However, if we focus on obsolescence as the business case we fall into a trap," said Wheadon. "The characteristics of an obsolescence project are cost-driven, and so they focus on replacing or upgrading only what you absolutely must have to address the obsolesce risk. But, doing no harm means no new functionality, and limits any automation improvements. Migration projects focused only on obsolescence risk will miss the opportunity to upgrade the control system and the control application to deliver more business value."
As a result, Wheadon reported that Dow Corning's process automation group added sales and marketing to its automation skills profile, so participants could justify and show the value of improving automation, instead of merely replacing it. "Talking about operator graphics doesn't add value," said Weadon. "You have to show what it means for the overall business. You have to speak business language to convince management that automation is a good value."
Finding real costs and benefits
To stop running in place and break out of obsolescence and maintenance limbo, Dow Corning worked with Siemens Industry and the University of Maryland's Center for Advanced Lifecycle Engineering to help understand the variables impacting the costs and benefits of control system migration decisions.
"We created a simulated model of our installed control system assets that modeled more than 25 years of operations, allowing us to perform sensitive analysis of key variables and parameters," said Wheadon. "The cost side is all the control system aspects and the benefits is 'what does it mean' to the plant.’"
The model consists of typical process control costs, such as:
- System price, including hardware and system software, cabinets and instruments, system design, instrument design and electrical design;
- Application engineering and programming costs, including automation requirements, control configuration, recipe development, simulation and testing, special programming and software installation;
- Installation costs, including E/I construction, checkout, commissioning, start-up and production outage;
- Annual engineering costs, including training, expansions, version upgrades, modifications and other improvements;
- Annual operating costs, including training, personnel, system power and vendor management; and,
- Annual maintenance costs, including training, personnel, spare parts and system management.
"When looking outside a narrow scope of an upgrade project, there where were a lot of hidden costs," noted Wheadon. "What does it take the company to maintain that asset for the next 25 years? We were maintaining 10 different control platforms across 25 worldwide manufacturing sites."
To complete its cost/benefit model and determine economic profit, Dow Corning had to subtract these expenses from the benefits side, which consists of:
- Annual manufacturing cost savings, including system availability, system failure rates, and system mean time to repair; and,
- Automation manufacturing value creation, including capacity, throughput, productivity, product quality and process safety.
"We had to look at the total costs and benefits of controls across our whole enterprise, but we couldn't do it if we were just looking at one upgrade project," added Wheadon. "We're not very good at looking at the automation value piece, so we had to begin by asking 'What could we do better if we had a chance?’ This was more than just replacing systems. Real automation value improves capacity and throughput, productivity, quality, and process safety."
Measuring the value of automation
Though the benefit side of the cost/benefit model only focused on capacity during the Dow Corning/Siemens/UMD study, it helped develop a three-part automation strategy.
The first part is upgrading control systems to address obsolescence risk. This must still be included with its known economic expenses and impacts, such as system costs, reduced maintenance and reduced risk of downtime.
The second part is improving levels of automation when upgrading a control system—adding real value to obsolescence projects—with specific improvements to operations. "Just taking the graphics and control code and running it on a new platform is not running the plant any better," said Wheadon. "We developed a business case to justify rewriting all the code for an application when we migrate an old system to Siemens. Our business model allowed us to throw it away and start again. Rewrite it and build in all the capabilities of the automation from the ground up when you do a migration project. Don't protect old code."
The third part is standardizing on one platform globally to reduce annual system costs and leverage constrained resources to deliver higher levels of automation. "The model helped us realize how much maintaining all the different platforms was costing us," said Wheadon. "It helped us build a business model to standardize on a single platform, and use our resources to deliver higher level of automation instead of managing different systems. After a market evaluation, we selected Siemens PCS 7 platform. For the last six years, as we replaced obsolete systems we migrate them to Siemens PCS 7, and use standard libraries everywhere, such as those for the S88 and S106 batch standards. We use standard architecture, standard security system, alarm management and training."
The automation value index
Wheadon cautioned that trying to directly measure the value of automation isn't easy because it impacts so many areas of manufacturing performance. "We struggled with how to measure the value of automation from more than just a capacity standpoint," said Wheadon. "Automation can improve productivity, quality and process safety, but how do we convince the business side of its impact? It was hard to show the value, so we took a different tack."
Consequently, Dow Corning developed a metric, the Automation Value Index (AVI), which correlates the level of automation with plant performance to help market and sell its business case for automation.
"Managers and accountant want something simple, so we came up with one number from 0% to 100% that everyone can understand," stated Wheadon. "The number was originally going to be called 'level of automation,' but we ended up with AVI index because nobody can argue with value. More value is always better."
The AVI correlates what the business or management side cares about—manufacturing performance—by using 10 aspects of control system design, implementation and operation that can positively impact plant operation. Manufacturing performance typically includes:
- Productivity measures, such as kg per $;
- Asset utilization metrics, such as overall equipment effectiveness (OEE) or total effective equipment productivity (TEEP);
- Quality measures, such as product predictability;
- Sustainability measures, such as BTU/kg or kg waste/kg;
- Safety measures, including incidents and audit KPIs;
- Maintenance costs; and
- Speed to market or time to market (TTM).
To gauge the business impact of automation, Dow Corning evaluates a unit against industry best practices in the following areas:
- Field devices and instrumentation,
- Basic controls,
- Sequential control batch (S88 and S106),
- Coding standards,
- Graphics and HMI design,
- Alarm management,
- MES/SAP integration,
- Asset management,
- Security, and
- Simulation.
For example, to calculate AVI for the alarm management category, Wheadon explained that Dow Corning multiplies its business-priority-based alarm management weighting factor of 13% by its alarm management assessment score of 60% by its service factor of 70% based on operator feedback, which results in a 4% AVI for alarm management.
"We had to come up with a number that relates automation to numbers that production understands," explained Wheadon. "We decided what good or best practice looked like and weighted each criteria for importance to production. All the weighted numbers were combined into a single number.”
"We also took a step back to see what types of automation are available today, what's good automation practice, and what components of automation will help unlock saving such as reducing startup time, production adjustments or process upsets. One example is the S106 standard for state-based control and managing outside of steady state. The batch concept includes startup, shutdown and maintenance operations. The ability to manage those with a new automation application makes a more efficient operation, helping consistency and capacity in the plant."
Wheadon added that addressing system obsolescence will continue to be a business necessity, and continue to be justified as the minimum investment needed to maintain reliable production. "However, a more proactive strategy can turn a business cost into a business opportunity," he said. "This means upgrading control systems to address obsolescence risk; improving levels of automation when upgrading a control system; and standardizing on one platform globally to reduce annual system costs and leverage constrained resources. Developing metrics like AVI that correlate level of automation with plant performance can help support the business case for such a strategy."
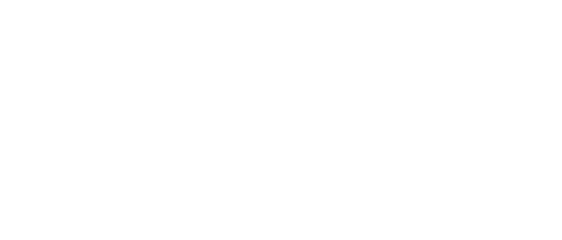
Leaders relevant to this article: