Brain drain is happening all over the world. In Europe and Asia, they lament that their best and brightest are moving to the U.S. Meanwhile, here in the U.S., we moan that our engineering and manufacturing jobs are moving overseas.
If you believe half the opinion pieces and editorials floating around, there must be a giant black hole somewhere in the universe that is sucking up all of Earth's brainpower.
Closer to home, the process industries are facing their own version of brain drain; but the engineering talent is not leaving this country, it's going idle or leaving the profession altogether. Process plants are laying off engineers and outsourcing work to service companies. Further, advances in control technologies and related IT and asset management technologies have, over the last several years, boosted individual productivity so much that a few can now do the work of many.
Experienced engineers (read: older), operators and technicians are leaving the ranks at a faster pace, either by retiring early, being retired early, or leaving the industry in search of greener pastures. There's also growing evidence that the process control discipline is not attracting the new engineering talent coming online. Not only are experienced brains draining away from process control, not as much talent is pouring into the pool either.
Process Plant Jobs Draining Away
"Some of our clients have cut deeply into their engineering departments," says Cliff Speedy, controls engineer at C&I Engineering, Louisville, Ky. "A number of the food and beverage plants we work in only have an engineering manager.
A chemical company manager in Tennessee agrees. "We are losing engineers at process plants," he says. "At my company we have fewer engineers. The situation is not dire, but it's not particularly enjoyable either. Fewer engineers are required due to productivity improvements enabled by automation and information technology. It would be nice if the technology made our jobs easier and we were able to keep all the people that were required with lesser technology. However, that is not the case, due to competition. As soon as one company reduces headcount, the rest are pretty much bound to follow."
Downsizing the engineering staff can be detrimental to plant operations. "The impact to the plant is that only what absolutely needs to be done gets done," says an anonymous engineer at a chemical plant in Michigan. "I am one of the last engineers at this manufacturing site who is in a traditional engineering role. There is an extreme focus on cost reduction all the way around."
We've heard this before. Plants no longer shut down for regular maintenance. Instead, they run for years at a time as maintenance problems pile up and the plant runs more and more inefficiently. Studies by Honeywell and Fisher Controls (Emerson Process Management) show that few control engineers have time to tune loops these days. They just let them run, as long as the plant doesn't blow up.To most engineers, none of this makes a bit of sense. Inefficient operations cost millions in excess energy, low-quality product and waste. Wouldn't it be more cost-effective to keep engineers on staff? Not to an accountant.
Part of the problem appears to stem from the fact that engineers and chemists no longer play as important a role in managing and operating process plants. The accountants and lawyers hold sway now, and have less of a professional stake in the work process engineers do.
"The accountants want to reduce the number of employees," says Glenn Givens, PE, at Innovention Industries in Burlington, Ontario. "They measure the value of these employees by their salaries. They cannot measure the relative benefit that each employee provides to the company so they assume that each employee in a given class provides the same benefit and has the same worth. Therefore, the accountants try to retire older, more experienced engineers and technicians and replace them with younger cheaper ones. They cannot measure the cost of the loss of experience."With all due respect to Mr. Givens, there's little hard evidence that there is a campaign against older process engineers. Staff cuts in the U.S. appear to be across the board, with no widespread discrimination. That may also be because of salary compression here in the U.S., where fledgling engineers have starting salaries roughly comparable to that of grizzled veterans.
"My former employer (a paper company) is apparently looking at engineering more and more as a commodity to be bought in the open market," says Tom Burger, owner of Burger Engineering, Camden, AR. "They are only hiring engineers to be production and maintenance managers, not engineers."
Invensys has studied the problem in depth. They commissioned a study of customers and did some market research, mainly because the brain drain affects how they sell systems.
Loss of key individuals and their knowledge is a major concern within the process industry, according to the company's research. "Two major factors contributing to this are downsizing and retirement," says Neil Cooper, director of strategic marketing at Invensys. "In the case of downsizing, senior engineers are being let go in an effort to reduce costs. But is this really effective? The people who keep production processes running smoothly are now gone. This significantly raises the risk of plant outages as well as injuries and environmental issues including the personal liability that plant managers now face under new legislation." What's the cost of an engineer compared to the cost of outages? As Cooper puts it, "If your plant is down for three hours, how many hundreds of thousands of dollars have you lost?"
The problems created by downsizing are compounded by the retirement "bubble," where a significant base of critical knowledge is walking right out the door when senior process engineers retire. "We estimate that 20-30% of what is considered the core knowledge staff within process industries will retire within the next 5-10 years," says Cooper. "This is particularly prevalent in the 'brown field' environment in North America and Europe."
NASA is having the same problem: a large percent of their experts are retiring. Over the next five years, one-fourth of NASA employees will become eligible for retirement. "NASA is on the brink of losing the talent it has," says Rep. Sherwood Boehlert (R-NY), chairman of the House Science Committee. He is also chief sponsor of the legislation, "NASA Flexibility Act of 2003," which will give the space agency more flexibility in hiring new engineers and scientists.
Outsourcing May Not Work
A shortage of onsite engineers in the process industries means that plant management has to contract with outside companies to get work done. "While it provides us an opportunity for work, it can be a source of friction for us later in the project," says C&I Engineering's Speedy. "It's difficult to ascertain the needs and wants of a client without a technical resource at the plant, and it is near impossible to turn over complex systems unless there is a competent person on site."
"We estimate that 20-30% of what is considered the core knowledge staff within process industries will retire within the next 5-10 years." --Neil Cooper, Invensys
In essence, process plants are downsizing, laying off experienced personnel, and relying on a single engineer to manage everything from process control to maintenance. We don't really have a brain drain in process control; instead, our best engineers are being put out to pasture. When those with in-depth site-specific knowledge leave the plant, chaos can reign, especially in older plants.
"Engineers and technicians that started when these plants were built around 30 years ago are now retiring," explains Cooper. "These are the people that were there when the facility was new and operating at peak efficiency. They've witnessed plant modifications and have seen the operations work day after day. They know the intricacies of the plant, how to optimize operations, and what certain readings and indications really mean."
Solutions to deal with this problem include artificial intelligence or expert systems that embody the knowledge of engineers long gone; process simulation software; and automatic loop tuning software that identifies bad loops.
"Emerson, Honeywell, Matrikon and even OSIsoft try to sell them software that does this," says Kennedy. "Personally, I think it is like most advanced control: it is not an algorithm issue, it is a 'lack of knowledge' issue. Most of this tuning software is not as successful as the original project in this area, done at a paper company several years ago. It simply listed the most offending loops every morning so that the people could better organize their work day."Unfortunately, the productivity and cost-reduction-induced brain drain has pulled process control wizards out of the plants, so there's nobody left to find the loops, let alone fix them.One solution the accountants adopt is to outsource engineering, maintenance and repair. Unfortunately, you can't outsource the kind of knowledge that comes from on-site experience. "For example, a technician observing an unexplained rise in a process temperature reading can deduce what the problem may be, based on experience," says Cooper. "He may know that an unseasonably hot day outside will affect process temperature readings, which can result in the process fluid not heating up to the temperature set point, which causes flow errors. These experts have the embedded knowledge of the process, and that's what is walking out the door."Outsourced services may not be very good, according to several readers. "I am very fortunate to work for a company that is not cutting back, but we never overextended to begin with," says Danny Justice, a maintenance supervisor in Brighton, Mich. "We have no degree-holding engineers, and our self-taught engineers and techs can go toe-to-toe with most degreed professionals. When we can't, we then bring in a 'professional.' Many times, these professionals are way less experienced than we are. It is very rare these days to find a tech or engineer that is trained, educated and experienced." Mike Lord, reliability engineer at Thiele Kaolin, in Sandersville, Ga., agrees. "The problem is finding people who know how to do the job," says Lord. "We tend to get inexperienced people.""Our automated system sorts and ships 500,000 cases a week," continues Justice. "We know how to tune, improve and monitor our system like no one else. We also take full responsibility when it fails. I cannot begin to describe how discouraging it is to call on 'outside help' only to get a highly educated, yet inexperienced technician that could not find his way out of a paper sack."Tough words, but based on bitter experiences. It's especially frustrating when you have to shell out scarce budget to pay for such "help." "There is always the issue that contract employees are not as familiar with your plant as you are," explains our anonymous process engineer in Michigan. "But they get paid for every hour worked. So, with a contractor it often costs more to do the same thing."Some contractors have begun to hire foreign-born engineers who are willing to work for lower wages. We know that at least one distributed control vendor is bringing in service reps and techs from , well, let's just say third world countries, to keep from offending anyone.This comment from a chemical engineer who works with "guest" process engineers on a regular basis is fairly typical: "The problems I encountered were unbelievable," he says. "My evaluation was not of just one or two engineers, but rather of 20 or 30. They all knew the basic concepts but had trouble implementing an organized solution in a reasonable amount of time. Most times they would not arrive at the correct solution and our process problems were exacerbated. I really have my doubts about companies looking to rely on resources from outside the U.S. From what I gather from other engineers in the industry, most of the time the work has to be re-done anyway. Yes, up-front engineering capital costs may be lower, but in the long run the cost is the same, if not more."We've heard all this before, from control engineers and IT professionals, so we agree with him: Companies who expect to save money by hiring engineers from off-shore, or outsourcing to companies who use them, may be making a huge, expensive mistake.On the other hand, we all know foreign-born engineers who are talented professionals, and are as qualified as any North American or European engineer. They've been in North America for years, and some have started up well-known companies. The International Black Hole
Brain drain is a worldwide problem. According to the European Commission, the European Union (EU) continues to lose its best brains in science and technology to the U.S. The EU's latest report, "Key Figures on Science, Technology and Innovation," issued in November 2003, reports that 71% of European-born U.S. doctorate recipients who graduated between 1991 and 2000 had no specific plans to return to Europe, and more and more are choosing to stay in the U.S. The most important reasons keeping European scientists and engineers in the U.S. relate to the quality of work here. Better prospects and projects and easier access to leading technologies were most often cited in the EU report as reasons to stay. It's not just Europe that's complaining. Australia, Africa, The Philippines, India, China, and other countries lament that they send their people to the U.S. or Canada to get an education, and the students don't come back. Until recently, we were happy to have them. Anyone who attended engineering school in the past 30 years knows that if wasn't for foreign graduate students, we wouldn't have had enough teaching assistants to go around. But seriously, when foreign graduates joined the U.S. or Canadian workforce, they filled a need and did an excellent job.But the dynamics have changed. On the one hand, North American companies are moving operations off shore to develop production closer to emerging markets; at the same time, the companies are bringing in rank-and-file engineering staff under H-1B and L-1 visas at lower pay scales to work in domestic plants.Interestingly enough, foreign workers living here are experiencing brain drain in reverse. According to WBAI Pacifica Radio (August 1, 2003), American companies starting up operations in India were actively recruiting experienced Indian workers at an engineering job fair in California. One company was seeking physical design, senior application, and R&D engineers. Also, like many of us, foreign students can't find seem to land an engineering job that offers a competitive wage here when they graduate, so they are returning home. Veterans Back On the Job
There is one excellent source of outsourced labor: the engineers and techs that were laid off or took advantage of early retirement. Frequently, these veterans are brought back in when the plant needs help, or when systems integrators hire them. Burger says current trends are helping his consulting business. "I had 20 years with a pulp-and-paper manufacturer, which often gives me a leg up on the competition that seldom has engineers with actual experience running a facility," he says."My former employer is in its third round of job cuts, including engineers, since I left in January 2001," says Burger. "That is why several of its plant engineers are looking to hire me on a temporary basis to help out during crunch times. This keeps their headcount down to please management."Systems integrators and service firms often snap up people who have been let go. "We are a full-service firm, with 60 or so PEs in five different disciplines, and this does indeed happen a lot in our process department, especially with engineers from refineries," says Speedy. "We have six or seven individuals that have been 'retired' from their previous employer. We snatch up those we can."Unfortunately, Speedy doesn't think many control engineers are as versatile as they once were. "In the control industry, you tend to find someone whose experience is limited to their old company's business, whether it's a single DCS manufacturer or a thermal processing expert from a juice plant," he explains. "It is difficult to find a well-rounded individual, possessing experience with programming and instrumentation, with a good base knowledge in electrical design. They tend to stay busy."Lessons from Farming
White collar work is fast going the way of manufacturing and farming, says Richard Sampson in his paper, "Surviving the Great Global Brain Drain."
In 1900, it took almost 40% of the workforce to grow America's food, but today"thanks to progressive mechanization, it takes less than 2% of the population.
He sees the same thing happening to white-collar jobs. "Most jobs as we know them are being transferred into all-electronic systems," he says.
He says we are only less than 5% "into" the new information age. On the horizon are grid computing, which will turn the Internet into a giant supercomputer; artificial intelligence, which will begin competing with college professors, biotech researchers, investment advisors, and other experts; self-aware computers, which can monitor and repair themselves; and nanotechnology, which will accelerate automation at warp speed.
"By 2100, it is possible that fewer than 2% of the work force will be needed to handle today's know-how functions in factories, stores, professional suites, research labs and universities."
Looks like a bleak future for engineers. Download the entire paper at: http://www.newagecitizen.com/PDF/braindrain.pdf
Finding New Control Engineers
Offshoring and outsourcing has put many control engineers out to pasture, and this is not helping the image of our profession. Young people don't see process control as a future career, and no one is encouraging them to take it up.We asked our readers if they would advise their children to enter process control. In most cases, they said they would recommend engineering, but not process control. We are in terrible shape as a profession if we ourselves are warning our own kids away from it.
It is indeed a shame that the future of our profession has to be built on the hope that things will turn around. As we pointed out in Control Report ("Love Those Street Racers," CONTROL, Sept. 03, p41), young hot rodders are learning data acquisition, controls, and sensor technology to build fast cars. Entering our profession should be a natural offshoot, but few do. Alas, no one is promoting our profession to the youth of America. So what's the solution to counteract these trends, to find the missing engineers, and renew the "gene" pool before all the process engineering talent drains away? There is growing evidence that plant off-shoring to cut labor costs is not the end-all, be-all for long-term cost savings. It's also an election year and both candidates have picked jobs as a primary campaign issue, with more and more in Congress addressing the problem by proposing corrective legislation. It is indeed a shame that the future of our profession has to be built on hope that things will turn around. But the forces of consumerism and other economics that are driving plants offshore, eliminating engineering jobs, and causing a brain drain in the process industries are far beyond our control. |
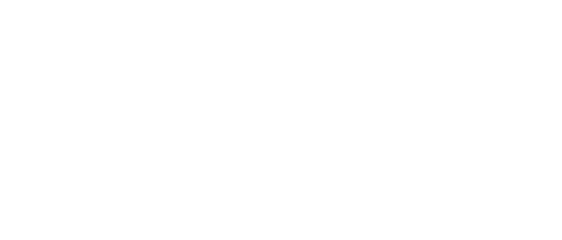
Leaders relevant to this article: