Software for auto tuning and adaptive control provide the opportunity to identify key loop dynamics besides providing a sound fundamental and automated basis for getting the best PID settings. Presented are uses of the knowledge gained and the setup of the automation system and testing/monitoring of PID performance to get the best results.
Overview
The relay method of auto tuning can provide a quick estimate of the ultimate period and ultimate gain and consequently the PID tuning settings in about three oscillations. The ultimate gain can provide an estimate of the gain margin if taken as the maximum gain for stability for a proportional-only controller. The ultimate period can be extensively used for the analysis of tuning settings, loop interaction, cascade dynamics, dead time versus lag dominance and disturbance dynamics. The ultimate gain and ultimate period can also be used to get initial tuning settings via the Ziegler Nichols ultimate oscillation method that is modified to provide more resilience to changes in process dynamics and to make the closed loop response less oscillatory. The modification consists of simply dividing the ultimate gain by the desired gain margin. Since most adaptive control tuners identify process models from a closed loop response benefit from a reasonable estimate of tuning settings and a non-oscillatory response, a good practice is to use the relay tuner with a gain margin of 4 or more to get the initial tuning settings in the ball park.
For dead time dominant loops, the factor applied to the ultimate period from the relay method to get the reset time could be reduced to provide a faster closed loop response test. The factor applied to the ultimate period can be reduced from 1 toward ¼ as the ultimate period decreases from 4 to 2 times the dead time to provide more aggressive integral action as the degree of dead time dominance increases.
The user is often over concerned about oscillations not realizing the attenuating effect of large process time constants or the slowing effect of very small integrating process gains. When an operator is asked point blank what step size is permissible, the step size cited is typically too small. A joint decision by operations and process engineering after a review of the historical data provide much more useful step sizes. Note what process excursions are acceptable and the associated changes in the PID output. Realize that statements made before analysis are difficult to reverse due to ego, a conservative mindset, and a lack of understanding of how dynamics attenuate and camouflage changes in process inputs.
Find from tuning tests at various setpoints, production rates, and batch or run times whether tuning should be scheduled based on the process variable or time for operating point nonlinearities or the PID output for final control element and process nonlinearities. Consider the use of signal characterization for operating point nonlinearities and nonlinear installed characteristics to free adaptive control to concentrate on unknowns and other nonlinearities. For pH the input signal characterization involves the translation from the ordinate to the abscissa of the titration curve so that the PV of the PID is percent reagent demand instead of pH. For final control elements, the output signal characterization translates the ordinate of the installed flow characteristic to the abscissa so that the manipulated variable is no longer signal but percent flow demand. A percent reagent or flow demand rather than engineering units is preferential. The actual pH and valve signal must be displayed and historized for operations and maintenance to enable diagnostics and analysis of the automation system and process performance.
A goal of less than 10% error in tuning settings from data compression and data update is advisable. Wireless transmitter default update rate and trigger level are set accordingly. Similarly, the PID module execution rate and transmitter damping and PID signal filter effect on the PID tuning settings is targeted to be less than 10%.
Recommendations
1. Ensure data compression is less than the smallest of the final control element and measurement resolution and sensitivity limits and the compression divided by the maximum rate of change of the signal is less than 10% of the total loop dead time or reset time setting whichever is smallest. Basically this amounts to turning compression off for most loops.
2. Ensure data update time is less than 10% of the total loop dead time or reset time setting whichever is smaller.
3. Set the module execution time to be less than 10% of the total loop dead time or reset time whichever is smaller.
4. Set the transmitter damping or filter time setting just large enough to prevent the valve or variable speed drive speed from changing due to measurement noise. The transmitter damping and filter time setting should be less than the 10% of the total loop dead time or reset time whichever is smaller.
5. Review historical data with operators and process engineers and decide on largest possible change in PID output that will not cause an unacceptable variability.
6. Choose a PID structure of PI on error and D on PV if setpoint response is not important and all disturbances are a process input rather than a process output. Take into account the significant filtering effect of intervening process volumes.
7. If both the load and setpoint response are important, use two degrees of freedom (2DOF) structure (e.g. beta=0.5 and gamma = 0.25) or a setpoint lead-lag (e.g. lag time = reset time and lead time = ¼ lag time).
8. Specify the process to be integrating for lag dominant self-regulating and runaway processes and choose test time to be at least four dead times plus two secondary time constants to save on test time and to enable integrator tuning rules.
9. Review the supplier documentation and presentations and attend short courses on the use of auto tuner and adaptive control software.
10. Use an auto tuner or open loop tests to get ball park tuning settings. For near and true integrating processes, you just need to identify the dead time and ramp rate.
11. Use a step size in PID output that is proportional to the PID gain with a minimum step size that is at least 5 times larger than valve or VSD deadband and resolution limit. Loops with a PID gain greater than 5 probably have near integrating or true integrating process dynamics. Selecting an integrating process response in the auto tuner or adaptive control setup and using a step size of at least 10% will greatly shorten the test time.
12. For temperature control of large liquid volumes (e.g. reactor and distillation columns), identify the secondary time constant associated with heat transfer surfaces or the thermowell via the use of special software. The identification package for some auto tuners and most model predictive control offer this ability. Consider the process dynamics to be near or true integrating so that only the initial response needs to be identified. Make sure the PID rate time is equal to the secondary time constant or ½ the total loop dead time, whichever is largest. For processes with positive feedback (e.g. highly exothermic reactors), the identification may need to be done closed loop so that the temperature control can stay in automatic to prevent a runaway reaction.
13. Do tests at several different setpoints and production rates to check performance and determine operating point (PID input) and feed (PID output) nonlinearities.
14. Use signal characterization on the most severe and relatively fixed nonlinearities to free up adaptive control to concentrate on unknown and variable nonlinearities and to make the results much less dependent upon step size and direction.
15. Use adaptive control to identify and correct for changes in process dynamics. For PID controllers with a severe process nonlinearity (e.g. pH control), schedule the tuning settings based on the process variable. Otherwise, schedule the tuning settings based on PID output to take care of production rate nonlinearities (e.g. increase in process gain and dead time as production rate decreases) and the valve gain nonlinearity due to the change in the slope of the installed flow characteristic (e.g. flattening of characteristic at low and high valve positions).
16. Use simulation (e.g. Simulate screen in Auto Tuner) to determine the effect of changes in tuning settings on load response and setpoint response. Note that the simulation may not include the effect of setpoint lead-lag. Decrease gain margin by increasing PID gain to decrease integrated absolute error (IAE) and rise time. Increase phase margin by increasing PID reset time to reduce overshoot.
17. Evaluate load disturbance response by making a step change in the PID output with the PID momentarily in manual if PID loop is allowed to go into manual. Do this is both directions. To reduce peak error, increase the PID gain.
18. Evaluate setpoint response by making a step change in the PID setpoint. Do this in both directions. To reduce overshoot, increase reset time or decrease beta in a 2 degrees of freedom PID structure or increase the lag time in setpoint lead-lag.
19. Periodically run tuning tests to look for deterioration in process and sensor dynamics with time (e.g. fouling of heat transfer surfaces and electrodes or loss of catalyst activity with continuous run time or batch cycle time). Schedule tuning settings and maintenance procedures based on these changes in dynamics.
20. Use pattern recognition and heuristic rules to evaluate the balance between proportional, integral, and derivative mode contributions to the output. An increase in reset time is stabilizing and thus permissibly done automatically via an adaptive reset set of rules based on whether future process variable values indicate an impending faltering (hesitation) or an overshoot in the approach of the process variable to a new setpoint or return to an existing setpoint.
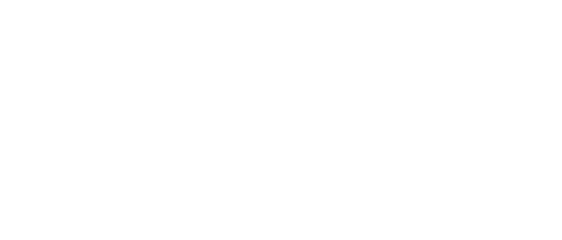
Leaders relevant to this article: